The Client
The client is a leading family-owned dairy product manufacturer with an annual turnover of USD 240 Million and 30+ years of experience. They are procuring milk from more than 2.5 lakh farmers and have the capacity to handle 16 lakh liters per day. The client is a strong community-focused organization which envisions to be the leader in the dairy industry making health a top priority. It has the capacity to process 365 million liters of milk per year with the highest standard of dairy production.
The Challenges
The client had to deal with multiple complex and interdependent processes, which include procurement of raw milk, dairy production planning, dairy process control, quality management, sales order processing and distribution. It desired to integrate of all business processes on a single platform that would result in business growth while leveraging the processes, people, technology and information.
Thus, it desired a solution partner with strong expertise, experience and understanding of the entire business and technology; inline it with industry’s best practices to manage the entire end-to-end product planning operations of dairy production, which are critical to the client in becoming the industry leader. Moreover, it was essential for a food and beverage company to be fully compliant with food safety regulations. Thus, it was also expected to manage the client’s IT landscape in compliance with all food safety regulations, to safeguard quality and standards.
The Objective
With a vision to become a leader in the dairy industry, the client desired to transform the entire business process, product development and retail network capabilities of the dairy plant, in order to modernize their business, incorporate new technologies, integrate the core system, thus, staying competent in the market as well as deliver value to its customers and or consumers.
The Solution
JK Tech re‐engineered the current business processes of the client, within and beyond the organizational scope. Our team integrated all the critical business process through SAP Functional and Technical Services. We also helped the client with incident support, which included unplanned interruptions and reductions in the quality of IT service and enhancement of the applications. JK Tech Smart Dairy Solution helped in the milk procurement process with a customized price calculation method. It tracked the quality of milk and issued a receipt run time. For trackability, an automatic batch number was assigned which used to get updated with the stock and verified with the invoice. Batch management across all stages helped in demand planning, material valuation and managing shelf life expiry dates for finished products. The capability to track products at each stage helped the client in their Kanban workflow model by recalling any good which raises a quality issue.
JK Tech Smart Dairy solution helped the client to include sales trip sheets for route sales, auto delivery & billing and mass upload of sales documents. The end-to-end solution tracked returned goods and the stock movement. It also gave the flexibility to integrate with handheld devices, POS and legacy systems which eases client’s retail challenges. The integration of multiple business processes with SAP Functional Modules focussed on gaining control over all aspects of operation with the business and helped the client manage databases for different processes from a single unified system, thus improving business agility and eliminating business processes inefficiencies.
SAP ERP functional modules include:
- SAP Financial and Controlling (FICO)
- SAP Sales and Distribution (SD)
- SAP Material Management (MM)
- SAP Plant Maintenance (PM)
- SAP Project System (PS)
- SAP Human resource management (HRM)
- SAP Business Warehouse (BW)
Similarly, our team was also involved in SAP Technical Module which included:
- SAP BASIS
- SAP ABAP
Our team was responsible for installing, configuring, updating, migrating and troubleshooting any technical problem on the SAP system ensuring that the system runs smoothly. There were several complex and fragmented process flows that were addressed through ticketing support via SAP Solution Manager. This module helped them with managing the application lifecycle and providing them with functionalities like integrated content, tools, methodologies, etc. to implement, operate, monitor and support the client’s SAP solution. In addition, maintaining a stable retail network operation, sales and distribution processes were integrated with the finance system.
JK Tech Solution Footprint – Milk Procurement Process:
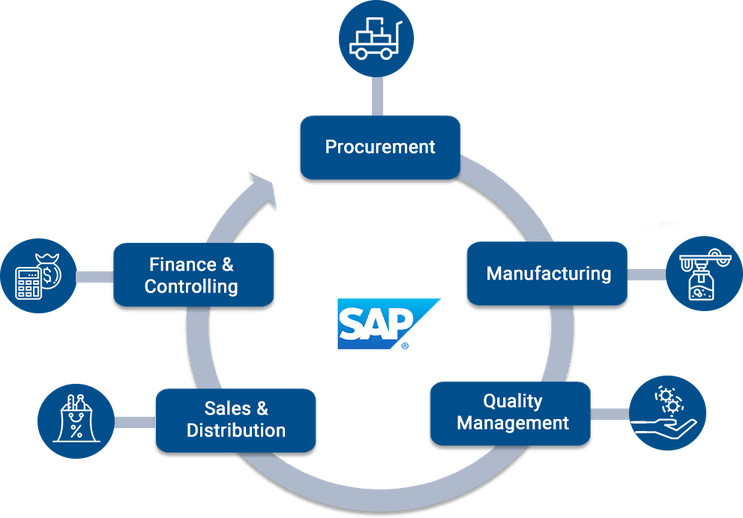
Overall, with the critical support by SAP-certified JK Tech Application Management Services, helped the client to get round-the-clock support and derive real business value from the engagement.

The Benefits
- The overall engagement resulted in a robust SAP platform with enhanced decision-making capabilities and analytical skills which steered the transformation journey of the client successfully.
- Streamlining of raw milk collection processes increased the operational efficiency of the business by reducing the number of milk procurement transactions (including the fat & SNF measurement) of farmers from 3,650,000 to 1000 per year.
- 100% payment to farmers through SAP solution.
- 100% end-to-end trackability and traceability resulted in simplified IT processes and calculation and monitoring of production cost were made easy with better tools. The product tracking ability was improved throughout the production and delivery cycle along with faster rollout through rationalization of core processes.
- Strong control over production planning operations resulted in the reduction of wastage losses by approximately 40%.
- The integration resulted in enhanced product visibility through a holistic view of the whole enterprise.
- The tailored solution helped the client to meet the challenges faced by the Industry reduce the implementation cost & timelines and be 100% compliant with Food safety regulations.